
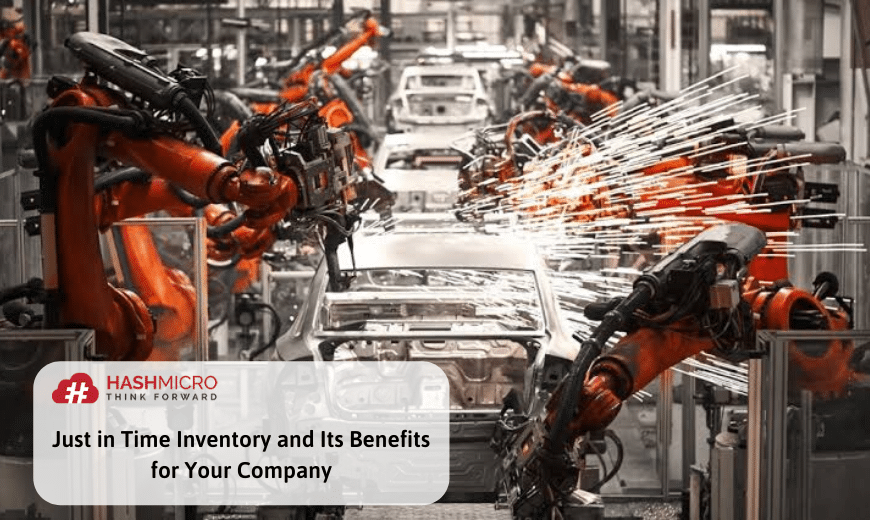
Lean manufacturing refers to the process of eliminating waste in the production process by identifying what adds value and what doesn't add value. However, they are different concepts that work together. Lean manufacturing, the Kanban system, and JIT system are often confused as the same thing. JIT, also nicknamed Toyota production system, is a complete opposite from the Just-in-case strategy that involves a manufacturer stocking inventory just in case there is an unexpected peak in production demand from customers. The components required to manufacture the cars arrive just as they are needed. This system typically relies on long-standing contracts within the local supply chain to deliver the different parts it needs to assemble an automobile. Taiichi Ohno, the founder of automobile manufacturer Toyota, is credited as being the father of the JIT inventory management system. Just in Time (JIT) inventory management was first adopted and perfected in Japan in the early 1970s. What is the History of Just in Time Production? Small-lot (single unit) conveyance: Use a control system, such as a kanban (card) system (or other signaling system), to convey parts between work stations in small quantities (ideally, one unit at a time).“Tally boards” record and analyze causes of production stoppages and slowdowns to facilitate correcting them later. “JIT lights” indicate line slowdowns or stoppages. A quality at the source ( jidoka) program must be implemented to give workers the personal responsibility for the quality of the work they do, and the authority to stop production when something goes wrong. Require supplier quality assurance and implement a zero defects quality program: Errors leading to defective items must be eliminated, since there are no buffers of excess parts.Teams of competent, employees must have responsibility for their own work. Flexible Work Force: Workers should be trained to operate several machines, to perform maintenance tasks, and to perform quality inspections.
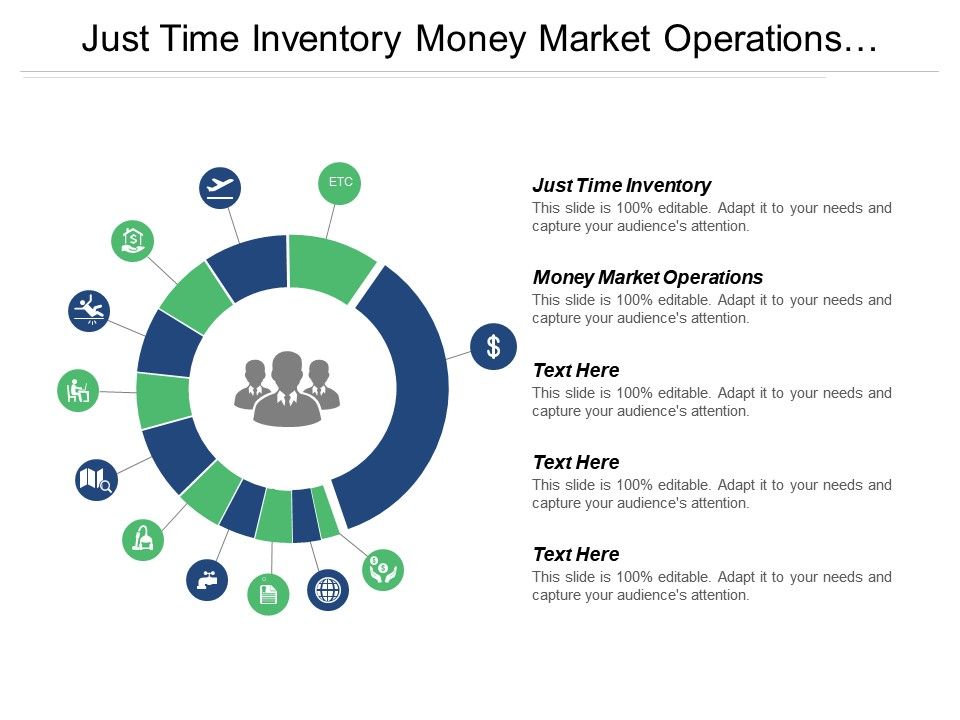
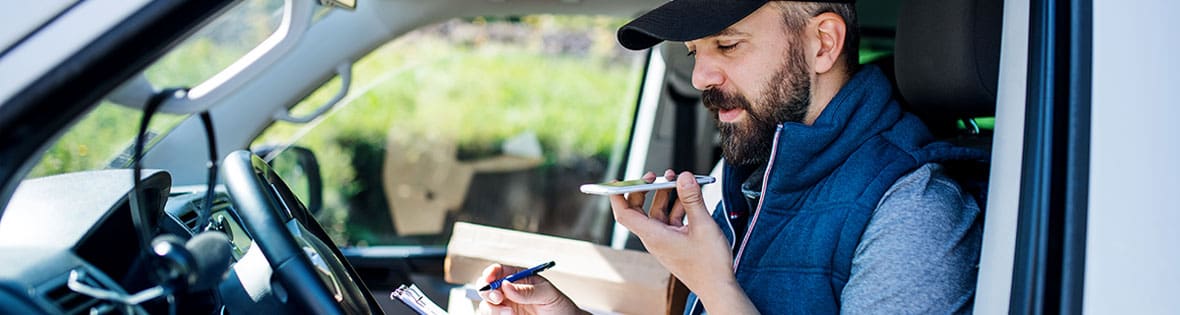
Also, establish a mixed model assembly to produce roughly the same mix of products each day, using a repeating sequence if several products are produced on the same line.
#Just in time inventory windows#
Establish freeze windows to prevent changes in the production plan for some period of time.
